Heavy Equipment Customer Value Agreements
Support you can count on
You can expect certain benefits in any Thompson Cat Customer Value Agreement on a new machine: delivered parts, an Equipment Protection Plan (EPP) and access to machine insights on your phone. Other aspects of CVAs adjust to what your business needs and how your operation works.
Convenience CVA
The right parts, delivered right on time, to the right place, with the maintenance instructions to help you get the job done right. The Convenience CVA fits operations who handle maintenance in-house, with security that protects you from unexpected costs with an Equipment Protection Plan. Schedule service and order parts, track shipments, manage maintenance events, perform inspections and view repair history, machine insights and results – all from the convenience of your phone.
Performance CVA
Bronze, Silver, Silver Plus, Gold, Platinum
On-time planned maintenance managed by Thompson Tractor. The Performance CVA introduces flexible dealer service so your crew can focus on work that drives revenue. It includes the elements of convenience, with your planned maintenance events and your EPP for Powertrain + Hydraulics + Technology lasting from three to five years.
Confidence CVA – TM & R
Added security with a Premier EPP that provides more comprehensive coverage, plus even more planned maintenance performed by certified Thompson Tractor technicians. The Confidence CVA helps protect your machine investment for up to five years (aligned with working hours). Similar to Performance, this CVA includes delivered parts, dealer service, Cat Fluids and machine insights on your phone. It also adds Condition Monitoring, which tracks machine health and detects upcoming problems or opportunities.
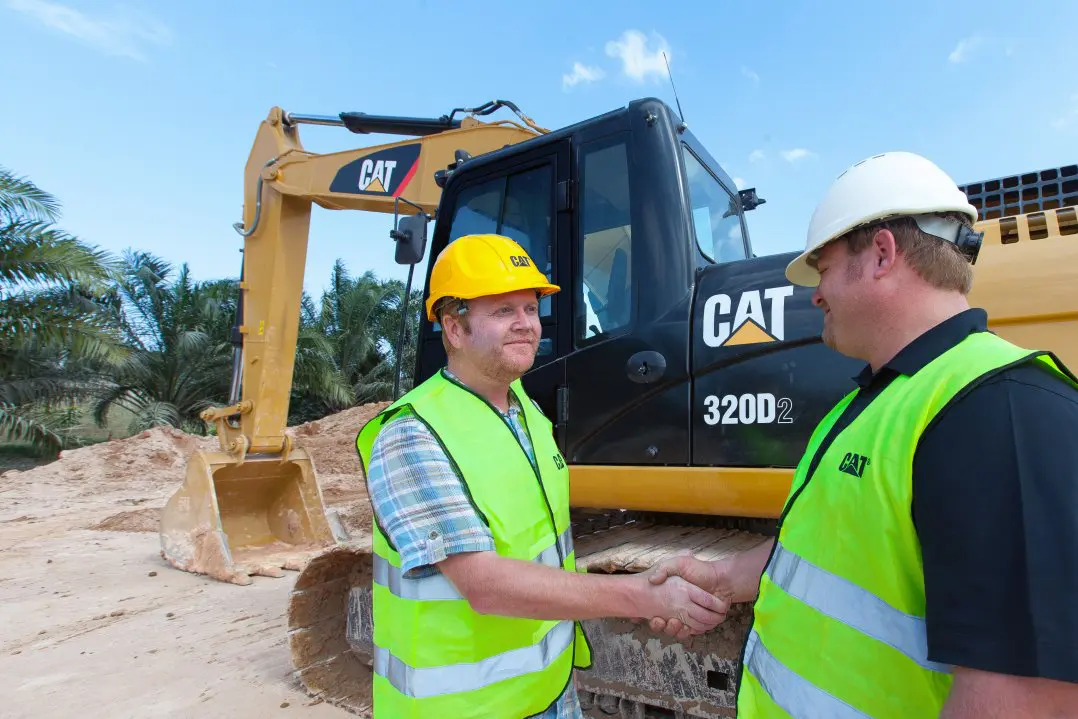
Extended Protection for Machines
Even the best built machines eventually need repairs, which always seem to happen at the worst time — right in the middle of a big job, when cash is tight or just after the warranty expires. An Equipment Protection Plan for a new, used or rebuilt machine:
- Provides coverage beyond standard machine warranty for parts and labor, and protects you from unplanned repair costs from covered defects in Cat material and manufacturer workmanship
- Offers multiple coverage options to fit your needs and budget
- Includes genuine Cat parts and service performed by factory trained dealer technicians
- Transfers with the machine when you sell it in the same region the EPP was purchased
Aftermarket CVA
Offers you hassle-free ownership of your not-so-new equipment to keep your machine easy to own and ready to work. Delivered parts. Flexible Service. Machine insights you can track on your phone. We can support any fleet size, as well as Cat and non Cat equipment.
Customer Value Agreements
HAVE QUESTIONS, OR NEED MORE INFORMATION? WE’RE HERE TO HELP!